Die Verkehrswende ist aktuell eine besondere Herausforderung für Unternehmen, Beschäftigte und die regionale Industriepolitik. Nach einer aktuellen Studie der Boston Consulting Group kommt es bis 2030 in Deutschland im Zuge der Verkehrswende zu einem Verlust von rund 220.000 Arbeitsplätzen in der Automobilindustrie. Allerdings, so die Prognose, wird erwartet, dass im Zuge der Transformation 205.000 andere Arbeitsplätze in anderen Bereichen entstehen. Der Umbau hin zur Elektromobilität hat in den vergangenen Jahren erheblich an Fahrt aufgenommen und die Endzeit der nicht-elektrischen Modelle ist absehbar. All dies setzt voraus, dass ausreichend Batterien zur Verfügung stehen und bietet für den Industriestandort Deutschland enorme Chancen, sich im weltweiten Markt zu positionieren! Ein Beitrag von Dr. Jens Katzek, Dr. Pascal Strobel und Thomas Lämmer-Gamp.
Der Dampfer fährt – und der Umbau zur Elektromobilität ist gesetzt
Auf Friday for Future Demonstrationen hört man ihn durchaus noch häufiger; den Satz, dass „die deutsche Automobilindustrie den Zug zur Elektromobilität verschlafen hat“. Aber wie so oft im politischen Geschäft halten sich knackige Slogans länger als die Realitäten. Spätestens seit die Entscheidung gefallen ist, sich von der Importabhängigkeit bei Batterien vom asiatischen Markt zu befreien, ist klar, dass es keine Umkehr mehr von der Elektromobilität geben wird – wenn wir es denn schaffen, rasch eine attraktive Ladeinfrastruktur aufzubauen, die für die Kaufentscheidung des Verbrauchers heute fast wichtiger ist, als die lästige Frage nach der Reichweite der eAutos.
Es dauert in der Tat seine Zeit, bis man begriff, dass das Pendant zur Motorenkompetenz der Vergangenheit – die man im Verbrennerzeitalter auf keinen Fall seinen Zulieferern überlassen wollte – in der Zukunft der eMobilität die Batteriekompetenz darstellt. Im April 2018 drängte die Politik immer stärker, sich in diesem Bereich zu engagieren. Der ehemalige Bundeswirtschaftsminister Altmaier forderte hohe Investitionen in Zukunftstechnologien, sowohl im Bereich der Elektroautos als auch bei den Batterien, die für diese Autos aus seiner Sicht am Standort Deutschland gebaut werden müssten. Im August 2018 erklärte VW dann, eine Batterieproduktion zu errichten, wenn sich dies finanziell rechnet. Gesagt getan: Bundeswirtschaftsminister Altmaier traf sich noch im September mit EU-Energiekommissar Maros Sefcovic in Brüssel und annoncierte, dass in Deutschland eine Batteriezellen-Fabrik gebaut werden wird, um im Wettbewerb mit Asien zu bestehen. Im Februar 2019 folgte dann die Bekanntmachung des Interessensbekundungsverfahrens zur geplanten Förderung im Bereich der industriellen Fertigung für mobile und stationäre Energiespeicher durch das zuständige Bundesministerium. Seitdem ging es Schlag auf Schlag und der Umbau hin zur Elektromobilität hat in den vergangenen Jahren erheblich an Fahrt aufgenommen.
BMW geht z.B. davon aus, dass im Jahr 2030 mindestens 50% der Fahrzeuge, die man weltweit ausliefert, vollelektrisch sein werden. Entsprechend wird das Produktionsnetzwerk für elektrische Antriebe konsequent erweitert. Daimler will bis 2030 in der Lage sein, nur noch vollelektrisch angetriebene Pkw zu verkaufen, „wo immer es die Marktbedingungen zulassen“. Der Volkswagen-Konzern will bis zum Jahr 2030 die Hälfte seines gesamten Modellangebots auf Batterieautos umgestellt haben. Dieses Ziel gab Herbert Diess im Juli 2021 bei der Vorstellung der neuen Unternehmensstrategie aus. Deutschland werde hier zu den Vorreitern gehören, sagte Diess: „Wenn wir bis 2030 in Europa 50 % batterieelektrisch anpeilen, werden wir in Deutschland dann schon auf 70 oder 80 %kommen„. Und Audi hat erklärt, dass sie 2025 ihren letzten neuen Verbrenner vorstellen. 2033 soll der Verkauf von nicht-elektrischen Modellen auslaufen (mit evtl. Ausnahme in China).
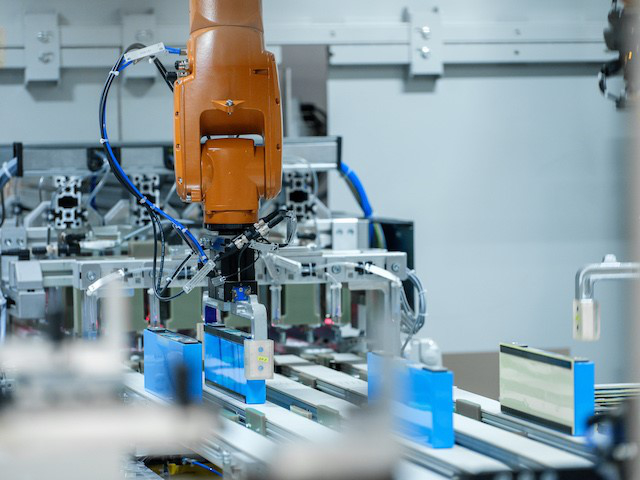
Das zentrale Leitthema des zukünftigen industriellen Sektors „Batterie“ stellt die Kreislaufproduktion) dar – und damit die Etablierung geschlossener Material- und Stoffkreisläufe auf Basis skalierbarer Produktionstechnologien. Dabei stehen aktuell drei Forschungsthemen im Fokus:
- die Verfahrenstechnik zur Batteriematerialherstellung und –konditionierung, nachhaltigen Batteriemassenformulierung sowie wissensbasierten Elektroden- und Separator-Herstellung,
- ökologisch und wirtschaftlich nachhaltige Batteriezellproduktion, die das Engineering, die Parametrierung und die Bewertung nachhaltiger Batterielebenszyklen ermöglicht,
- umweltschonende wirtschaftliche Recyclingverfahren als Basis für geschlossene Stoffkreisläufe.
Batterieherstellung ist eine Schlüsseltechnologie
In diesem Strukturwandel stellt die Herstellung der Batterien einen Schlüsselfaktor dar. Die industriellen Entwicklungspotenziale für Batteriezellfertigung in Deutschland werden dabei nicht nur durch den Umstieg in die Elektromobilität getrieben, sondern auch durch Unternehmen in zahlreichen weiteren Branchen, darunter der Energieversorgung und der Luftfahrtindustrie. Studien erwarten, dass sich der aktuelle Bedarf an Batterien in den nächsten zwei bis drei Jahren verdoppelt. Von Seiten der IG Metall wird davon ausgegangen, dass es bis 2030 in Europa zu einem Aufbau von Produktionskapazitäten auf bis zu 1.100 GWh pro Jahr kommt. Derzeit ist der Aufbau von 40 neuen Batteriefabriken in Europa angekündigt.
Die Wertschöpfungskette Batterie betrifft dabei eine Reihe von Industriezweigen. Die Prozesse entlang des gesamten Lebenszyklus einer Batterie ermöglichen es Unternehmen des klassischen Maschinenbaus, der Digitalisierungsbranche sowie von Start-ups an der Batterieproduktion teilzuhaben. Im gesamten Batteriezellherstellungsprozess ist nur ein kleiner Anteil (bspw. die Elektrochemie) nicht durch den klassischen Maschinenbau und die damit verbundenen Fertigungsverfahren abbildbar. Eine vorausschauende Industriepolitik unterstützt deshalb Unternehmen des klassischen Maschinenbaus dabei, zu identifizieren, in welchen Prozessschritten des gesamten Lebenszyklus einer Batteriezelle sie ihre herkömmlichen Fertigungsverfahren einsetzen können. Die Herausforderung dabei besteht auch darin ist, den Wissens- und Technologietransfer zur Sensibilisierung, Chancenerkennung und Befähigung effizienter zu gestalten.
Die Vielfalt der mit der Wertschöpfungskette Batterie verbundenen Einzelthemen spiegeln sich auch in den verschiedenen Kompetenzclustern im Rahmen des Dachkonzepts „Forschungsfabrik Batterie“ des BMBF wider, zu dem die Cluster „Batteriematerialien (ExcellBattMat)“, „Festkörperbatterien (FestBatt)“ und „Batteriezellproduktion (ProZell)“ gehören. Neue Batterie-Kompetenzcluster wurden zu den Themen „intelligente Batteriezellproduktion (InZePro)“, „Recycling/ Grüne Batterie (greenBatt)“, „Batterienutzungskonzepte (BattNutzung)“ sowie „Analytik/ Qualitätssicherung (Aqua)“ etabliert.
OEM setzen bei Batterien nicht nur auf Zulieferer
Wie oben beschrieben hat der Umbau hin zur Elektromobilität bei den deutschen Automobilherstellern erheblich an Fahrt aufgenommen. Das VW Werk im sächsischen Zwickau gehörte zum ersten, das seine Produktion im laufenden Betrieb 2021 vollständig von 300.000 Verbrennerautos auf 320.000 E-Autos umstellte. Für sein Batteriegeschäft gründet VW eine Europäische Aktiengesellschaft. Die neue Tochter solle alle Aktivitäten von der Rohstoffverarbeitung über die Entwicklung der VW-Einheitszelle bis zur Steuerung der geplanten sechs europäischen Gigafabriken übernehmen. Dazu gehören auch neue Geschäftsmodelle wie die Weiterverwendung ausgedienter Fahrzeugbatterien („second-use“) und das Recycling. Zentrum der Aktivitäten wird der Standort Salzgitter sein, wo im Jahr 2025 die Einheitszellen für das Volumensegment des VW-Konzerns gefertigt werden sollen. In der ersten Ausbaustufe soll die Fabrik 20 Gigawattstunden (GWh) Jahreskapazität produzieren. 40 GWh sind geplant. Insgesamt sind ca. 2 Mrd. € für Bau und Ausrüstung der Gigafabrik in Salzgitter vorgesehen. Perspektivisch sollen dort mehr als 2.500 Menschen beschäftigen werden – vornehmlich Mitarbeiter aus dem früheren (Verbrenner) Motorenwerk Salzgitter. Diese sollen mit Schulungsmaßnahmen auf ihre neuen Aufgaben vorbereitet werden.
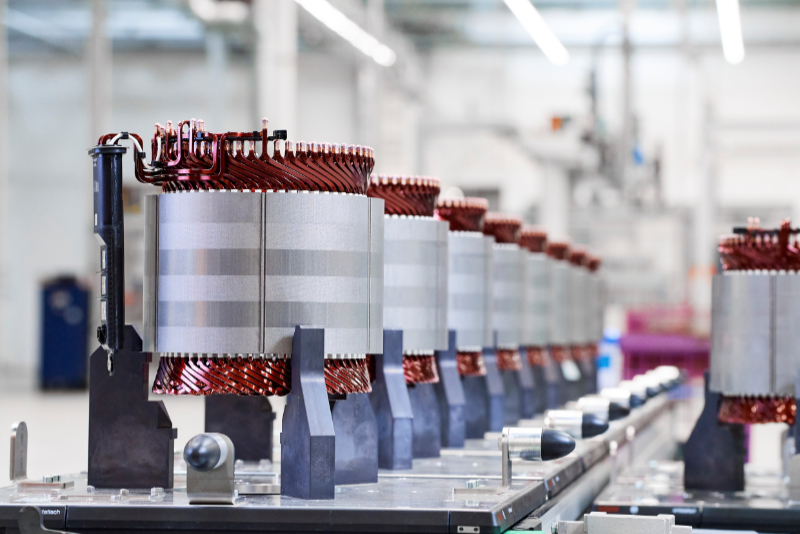
Die BMW Group produziert allein in Deutschland an drei Standorten Hochvoltbatterien und Batteriekomponenten: in Dingolfing, Leipzig und Regensburg. Das BMW-Werk in Regensburg begann bereits im April 2021 mit der Lackierung von Batteriezellen für Hochvoltbatterien. Die Zelllackierung erhöht die mechanische Robustheit und Wärmeleitfähigkeit der Batteriezelle. Ab 2022 werden dort auch Hochvolt-Batterien produziert. Das Werk in Leipzig, das bereits im September 2013 eine Vorreiterrolle mit der Produktion der mit Batterien vollelektrisch angetriebenen PKW-Modelle i3 und i8 inne hatte, hat die bereits bestehende Batteriemodulherstellung (aus zugelieferten Batteriezellen von CATL) in 2022 noch einmal durch eine Investition von über 100 Mio. € erweitert. Ab 2023 sollen dann im Werk 350.000 Autos produziert werden – statt der bisherigen ca. 230.000. Bereits in 2017 wurde eine Speicherfarm mit second-life Batterien und einer Kapazität von 700 Hochvoltspeichern eröffnet.
In Ludwigsfelde südlich von Berlin wird von Mercedes-Benz ab Mitte 2023 der eSprinter gebaut – mit der Batterieproduktstätte von Microvast nur wenige Kilometer entfernt. Das Unternehmen kündigte an, dass der Start der Produktion im Januar 2021 erfolgen werde. Zu Beginn sollen 100 Mitarbeiter im neuen Werk beschäftigt werden. Microvast plant zunächst eine Fertigungslinie aufzubauen. Als Kapazität gibt der Batteriehersteller 15.000 bis 30.000 Batteriepacks und 250.000 bis 300.000 Batteriemodule an. Die vorgelagerte Fertigung von Batteriezellen verbleibt zunächst in China. Microvast wurde 2006 in den USA gegründet. Die Zentrale befindet sich in Stanford, Texas, die Produktion seit 2009 in Huzhou, China.
Batteriemodule werden von Mercedes auch seit vielen Jahren in der 100%-Tochter Deutsche Accumotive im sächsischen Kamenz produziert. Auch Daimler suchte mit CATL eine Kooperation die Daimler Truck die Batterien für den Mercedes-Benz eActros LongHaul liefern. Der Elektro-Lkw soll 2024 in Serie gehen und mit einer Batterieladung rund 500 km weit kommen. CATL ist auch der Lieferant für die Batteriezellen des 2021 vorgestellten Oberklassewagens Mercedes EQS. Und dann ist da noch die Tesla Produktionsstädte in Brandenburg – die Ende März 2020 final eröffnete mit für 500.000 Einheiten größte Produktionsstätte für e-Fahrzeuge in Deutschland dar. Und die Planungen für eine Gigafactory für Batterien haben bereits begonnen.
Batterien: Ein neues Feld der Zulieferindustrie
Aber auch für die Zulieferindustrie sind die Batterieentwicklung interessant. Der Zulieferer Bosch fertigt seine 48-Volt-Batterien für Hybrid-Autos in Eisenach. In Serie baute Bosch die 48-Volt-Batterien bislang nur in China. Und die Firma Dräxlmaier hat in Sachsenheim bei Stuttgart bereits im Mai 2019 ein Produktionswerk für das 800-Volt-Batteriesystem des Porsche Taycan errichtet. Im Oktober 2020 feierte das Unternehmen dann Richtfest seiner Produktionsstädte nördlich von Leipzig, für die es ca. 50 Mio. € investiert hat und in dem ca. 100 Mitarbeiter beschäftigt werden sollen.
Kobaltfreie Batteriezellen zur industriellen Serienreife zu bringen, gelang als erstem der SVOLT in Überherrn im Saarland). Dort werden Lithium-Ionen-Batterien für Elektrofahrzeuge sowie Energiespeichersysteme entwickelt und produziert. Geforscht wird auch in Bereichen wie Festkörperbatterien und Trockenbeschichtung. Darüber hinaus arbeitet SVOLT an nachhaltigen Konzepten für das Recycling von Batterien und Batteriesystemen und plant den weltweiten Aufbau von bis zu 100 GWh Produktionskapazitäten für Batteriezellen. Im Saarland will das Unternehmen 2 Mrd. € investieren und beabsichtigt 2.000 Mitarbeiter einzustellen.
Auch die Altech Industries will im Lausitzer Industriepark „Schwarze Pumpe“ an der Grenze zwischen Brandenburg und Sachsen einen Produktionsstandort für die Beschichtung von Hochleistungs-Lithium-Ionen-Batterien errichten. Dazu sollen bis zu 500 Mio. € in das Vorhaben investieren werden und rund 150 Arbeitsplätze entstehen. Mit der speziellen Beschichtung soll, so Altech, die Reichweite von Elektroautos verdreifacht werden. Etwa 50 Kilometer weiter, in Schwarzheide, erreichtet die BASF ihre Prototypanlage für das Batterierecycling von Kathodenmaterialien.
Das chinesische Unternehmen CATL hat in Arnstadt am Erfurter Kreuz (Thüringen) rund 1,8 Mrd. € in seine Zellenfabrik zur Herstellung von Lithium-Ionen-Zellen für E-Akkus investiert. Mittelfristig sollen etwa 2.000 Mitarbeiter in einem der weltgrößten Zellenwerke Lithium-Ionen-Zellen für Elektroauto-Akkus produzieren. Und einen Großkunden hat CATL auch bereits: Der bayerische Autobauer BMW ist über sein chinesisches Joint Venture Brilliance an CATL beteiligt. Den bisherigen Planungen zufolge will BMW ein Drittel seines Akkubedarfs aus deutscher Produktion decken. Im Endausbau soll das CATL-Werk in Erfurt auf eine Batteriekapazität von jährlich bis zu 100 Gigawattstunden kommen. Das ist genug für 1,3 Mio. E-Autos mit einem 75 kWh-Akku an Bord, wie ihn etwa BMWs neuer E-SUV iX in Basisausstattung bietet.
Um in diesem Markt mithalten zu können arbeiten Zulieferer auch zusammen. So haben zum Beispiel ZF und CATL eine globale Partnerschaft geschlossen, um auf dem Aftermarket für Batterien ein Servicenetz, Schulungen und Recycling anzubieten – denn mit der raschen Verbreitung der E-Autos in den kommenden Jahren wird auch das dazu gehörige Aftermarket-Geschäft wachsen. Die mehr als 10.000 Werkstattpartner von ZF sollen das Servicenetz von CATL verstärken.
Das Batteriegeschäft umfasst mehr als nur die reine Produktion
Neben der Batteriezell- und Modulproduktion haben sich auch andere Zuliefererdienste etabliert. So hat in Barleben (Sachsen-Anhalt) die japanische HORIBA Fuelcon GmbH 30 Mio. € investiert, um ihren Standort mit Prüfständen für Batterien und Wasserstoffbrennstoffzellen auf 350 Mitarbeiter zu vergrößern. In Saarbrücken betreibt die CTC advanced eine große Prüfhalle für hochkapazitive Li-Ionen-Batteriesysteme und unterstützt Batterie- und Automobilhersteller bei der Qualitätssicherung. Ein weiteres Beispiel ist die Neways mit Standorten in Neunkirchen/Saar und Erfurt, die Batteriemanagementsysteme herstellt.
Auch der Multi Borg Warner investiert im Bereich der Batteriemanagementsysteme und beteiligt sich an dem in San Francisco ansässigen Unternehmen Qnovo, das Elektronik und Software entwickelt, um den Batteriezustand und Schnellladevorgänge zu überwachen.
Auch in NRW ist viel Dynamik zu beobachten. Immer mehr Zulieferer, die bisher keine Berührungspunkte mit dem Thema Batterie hatten, entdecken neue Geschäftsmöglichkeiten. So bietet die WKW.Group aus Velbert ergänzend zu ihrem traditionellen Angebot von Zier- und Funktionsteilen nun auch Strukturbauteile für Batterierahmen, Batteriekühlung und Batteriegehäuse an.
Und auch die Anlagenbauer stellen sich auf die neuen Gegebenheiten ein. Die Woll Maschinenbau in Saarbrücken entwickelt z.B. flexible Automatisierungsanlagen, die eine intelligente Produktion ermöglichen. Dieses Know-how wird im Bereich E-Mobility mit Produktionsanlagen für Batteriemodule, Montageanlagen für Elektro-und Hybridantriebe bis zur Produktionstechnik für die benötigten Komponenten, wie Solarmodule, Steckverbinder und Batterien eingesetzt. Ähnlich auch die Firma Lyric, die mit ihrem Know-how bei der kundenspezifischen Herstellung von High-End-Automatisierungsanlagen im Bereich der Batterieherstellung aktiv ist.
Batterien und Start-Up Unternehmen
Neue Chancen des neuen Marktes ergeben sich auch für innovative Start-Up Unternehmen, wie z.B. das aus der Schweiz kommende, 2019 im sächsischen Döbeln angesiedelte Unternehmen Blackstone, dass mit seinem additiven Verfahren Batterieelektroden und Separatoren für Lithium-Ionen-Batterien in 3D drucken will oder die DENKweit aus Halle (Saale), die sich mit der Qualitätskontrolle von Batteriezellen und Batteriemodulen beschäftigt.
Ein interessantes Beispiel für die Zusammenarbeit zwischen einem etablierten OEMs und einem Start-Up Unternehmen stellt die Cellforce Group GmbH dar, die Hochleistungs-Lithium-Ionen-Pouch-Zellen für Spezialanwendungen entwickelt und an dem die Porsche AG mit etwas mehr als 70% beteiligt ist. In der Entwicklungs- und Produktionsstätte in der Nähe von Tübingen sollen von 2022 an Hochleistungs-Batteriezellen mit einer Kapazität 100 MWh/ Jahr für 1.000 Fahrzeuge hergestellt werden. Der Produktionsstart für die Serie ist für das Jahr 2024 geplant. Interessant an dieser Kooperation ist auch der dritte Partner im Bunde. Denn die BASF wurde als exklusiver Zellentwicklungspartner für die Lithium-Ionen-Batterien der nächsten Generation ausgewählt. Im Rahmen der Zusammenarbeit stellt BASF besondere Kathodenmaterialien für die Batteriezellen zur Verfügung, die ein schnelles Laden und eine hohe Energiedichte ermöglichen.
BASF nimmt sich auch des Thema Recycling an. Die Abfälle der zukünftigen Cellforce Group Produktionsanlage werden in einer BASF-Prototypen-Anlage für Batterie-Recycling in Schwarzheide bearbeitet. Lithium, Nickel, Kobalt und Mangan werden in einem hydrometallurgischen Prozess recycelt und wieder in den BASF-Produktionsprozess für Kathodenmaterialien eingebracht, was wichtig ist, um den CO2-Fußabdruck künftiger Akkus zu verkleinern.
Die wirtschaftlichen Potenziale die damit einhergehen, hat das Fraunhofer-Institut für System- und Innovationsforschung (ISI) im Auftrag des VDMA untersucht. Die Experten gehen davon aus, dass 2030 in Europa jährlich Lithium-Ionen-Batterien mit 400 bis 900 Gigawattstunden Kapazität verbaut werden. 2040 sollen es 800 – 1300 GWh/ a sein. Das Aufkommen von Batterien, die nach der Nutzung in Fahrzeugen zum Recycling anstehen, sieht man bei ca. 230.000 to/ a im Jahr 2030 und sage und schreibe 1,5 Mio. to im Jahr 2040! Vorhanden oder geplant sind in Europa aber bislang nur Recyclingkapazitäten für 33.000 Jahrestonnen. Bis 2040 sind damit Gesamtinvestitionen in Recyclinganlagen von schätzungsweise 6,6 Mrd. € erforderlich.
Batterien und Forschungsbereich
Auch im Forschungsbereich gibt es eine Reihe von relevanten Playern wie das Batterieforschungszentrum in Jena oder die Fraunhofer-Institut in Dresden (IKTS und ISW). In Münster hat im November 2021 die erste Anlage des mit insgesamt 680 Mio. € geförderten deutschen Batterieforschungszentrums seinen Regelbetrieb aufgenommen. Ende 2022 soll das erste komplette Forschungsgebäude an die Fraunhofer Gesellschaft übergeben werden.
Die Batterieforschung in Niedersachsen ist wesentlich durch das Forschungszentrum Battery Lab Factory Braunschweig (BLB) und dem Fraunhofer Projektzentrum ZESS mit großer Expertise im Bereich der Batterieforschung geprägt. Und in Stuttgart wurde 2021 das Zentrum für digitalisierte Batteriezellenproduktion am Fraunhofer-Instituts für Produktionstechnik und Automatisierung (IPA) eröffnet, um u.a. mit dem Varta die Entwicklung von Batteriezellen durch eine Digitalisierung der Batteriezellenproduktion voranzutreiben.
Mit der Lebensdauer von Batterien beschäftigt sich ein Team an der Universität Halle um Prof. Wolfgang Binder, die Rahmen des EU-Forschungsprojekts „Bat-4-Ever“ sogenannte „selbstheilende Polymere“ entwickeln, von denen man sich erhofft, dass sie die Speicherkapazität von Lithium-Ionen-Batterien erhöhen und die Lebensdauer verlängern. Hierfür wurden Polymer-Materialien entwickelt, die kleinste strukturelle Defekte selbst erkennen und selbst reparieren können. Mit ähnlichen Themen beschäftigt sich die Bergische Universität Wuppertal, die z. B. nicht nur Alterungsprozesse von Batterien untersucht, sondern in verschiedenen Projekten auch an Fragen des Lademanagements sowie der Integration von Fahrzeugbatterien als Pufferspeicher in einem Smart forscht. All dies sind nur einige Beispiele, die zeigen, wie vielfältig sich die Forschungslandschaft zum Themenfeld Batterie ein Deutschland entwickelt hat und wir vielfältig damit auch die Möglichkeiten sind, neue und innovative Technologien durch eine engere Kooperation zu entwickeln.
Die Autoren:
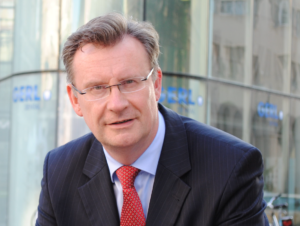
Dr. Jens Katzek, Geschäftsführer des ACOD (Automotive Cluster Ostdeutschland)
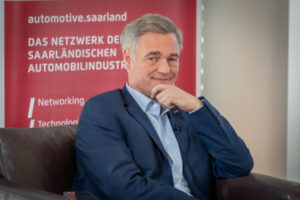
Dr. Pascal Strobel, Netzwerkleiter des Automotive Saarland
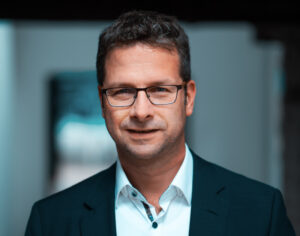
Thomas Lämmer-Gamp, Projektentwicklung automotiveland.nrw e.V.